From raw materials to finished products, I summarized the three points
Many people ask “what should I look for in a factory” and “how can I tell if a factory’s production is good or not”.
Indeed, these questions are really important for trading companies, purchasing agents and factories’ own sales, but no one seems to have shared the relevant topics.
So, according to my past 7 years in door hardware work, and in the process of work stepped in countless deep pits, summed up the refinement of the most important three elements to see the factory to share with you.
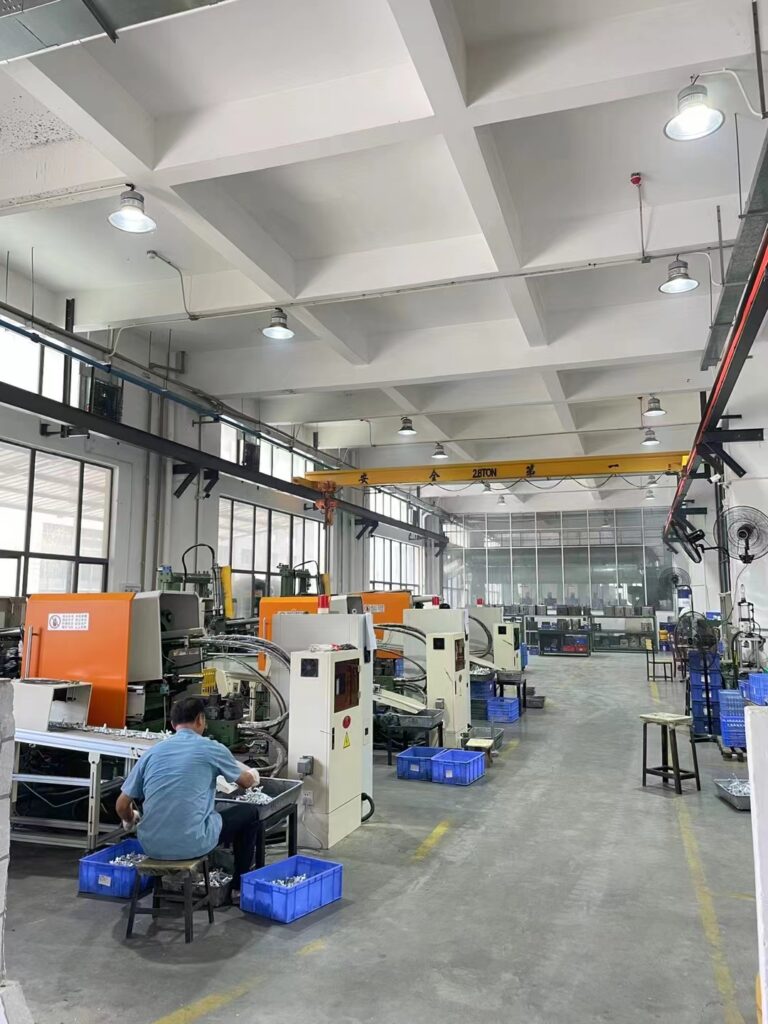
1. Incoming inspection specifications
The factory has no incoming inspection work, and whether this work is standardized, there is a very huge difference.
In many factories I have visited, there is no such thing as incoming inspection norms.
Upstream suppliers will send raw materials or components, symbolic unpacking to see, and then “okay no problem into the warehouse” or “if there are problems, then?”.
The essential reason behind this practice is actually the lack of production control in the factory and the neglect of the concept of “quality cost”.
The so-called quality cost means that quality problems occur in different parts of the supply chain, and their costs are different. The lowest cost is in the incoming inspection process, and the highest cost is in the goods on-the-shelf process.
Before starting cooperation, we need at least the other party to send us relevant documents (including but not limited to incoming material inspection standards, incoming material inspection records) to confirm that they do have the corresponding process and the real implementation, not just a paper on the factory wall documents.
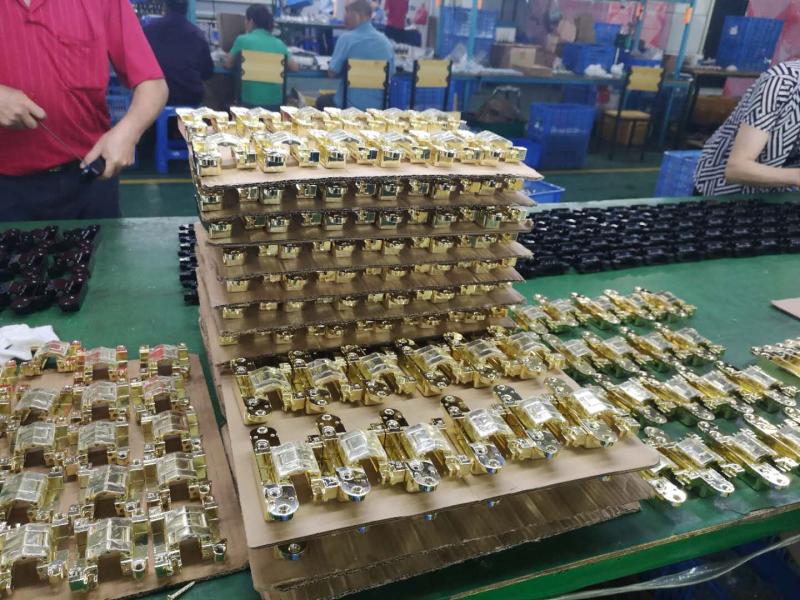
2. Production process control
Almost every factory will say “our product quality is good”, but from the perspective of supply chain managers.
First of all, what is the indicator to prove good quality?
After all, everyone’s perception of quality is different, and what you call good quality may not be in my opinion.
Second, what is your method of achieving this target?
What kind of production process did you adopt? How do you ensure that you get this target for each batch? How do you achieve reliability and consistency? (This is the “path” to achieve the “target”)
Finally, what are the specific methods, norms and standards for production operations at each process node? (This is the specific “measures” in the “path”)
All these are implemented into the whole production process, which is “production process control”.
In the process of factory inspection, the key is to confirm how the other party actually carries out the control of the production process in order to achieve the purpose of influencing the results.
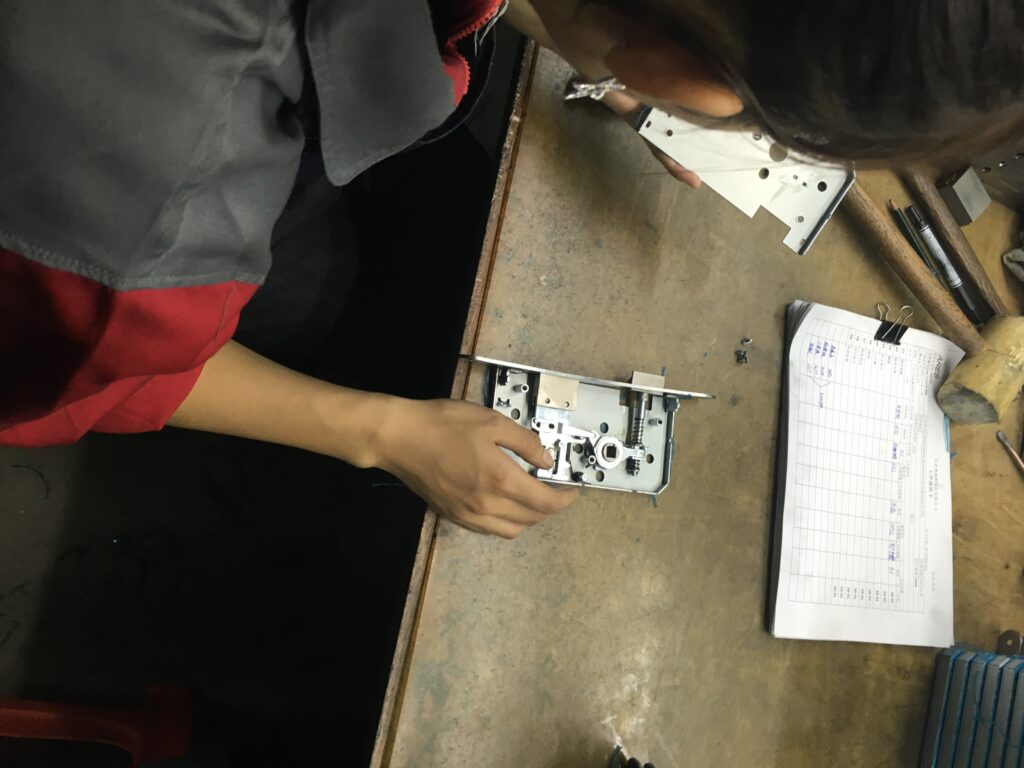
Every time I look at the factory, I will see whether the other party has “production work instructions” pasted on each post, and observe whether the other party’s production personnel operate according to the work instructions in the end.
As well as ask “your company’s production work is mainly done by teachers, or ordinary workers to complete”.
Some sales will be proud to say “most of our factory workers are experienced teachers”, but in fact, from the perspective of procurement and supply chain managers, this may not be a good thing.
The reason is simple: all procurement is risk averse.
Yes, it is true that an experienced teacher can do the job to 120 points. But what if the master takes a leave of absence, gets emotional, feels tired and distracted, and then replaces the job with a junior apprentice who has little experience? Will not instantly reduce the work to 60 points? You may say “ah, this is a small probability event”, but all the risks and accidents, which is not a small probability event to start with?
So factories with a sense of fine production never rely too much on the experience and sense of the teacher, but rely on the “production work instructions”.
No matter who you are, as long as you follow the instructions for operation, you may not be able to achieve 120 points, but definitely will not fall to 60 points.
In addition, also need to be wary of some factories with little use of the work instructions out to fool people.
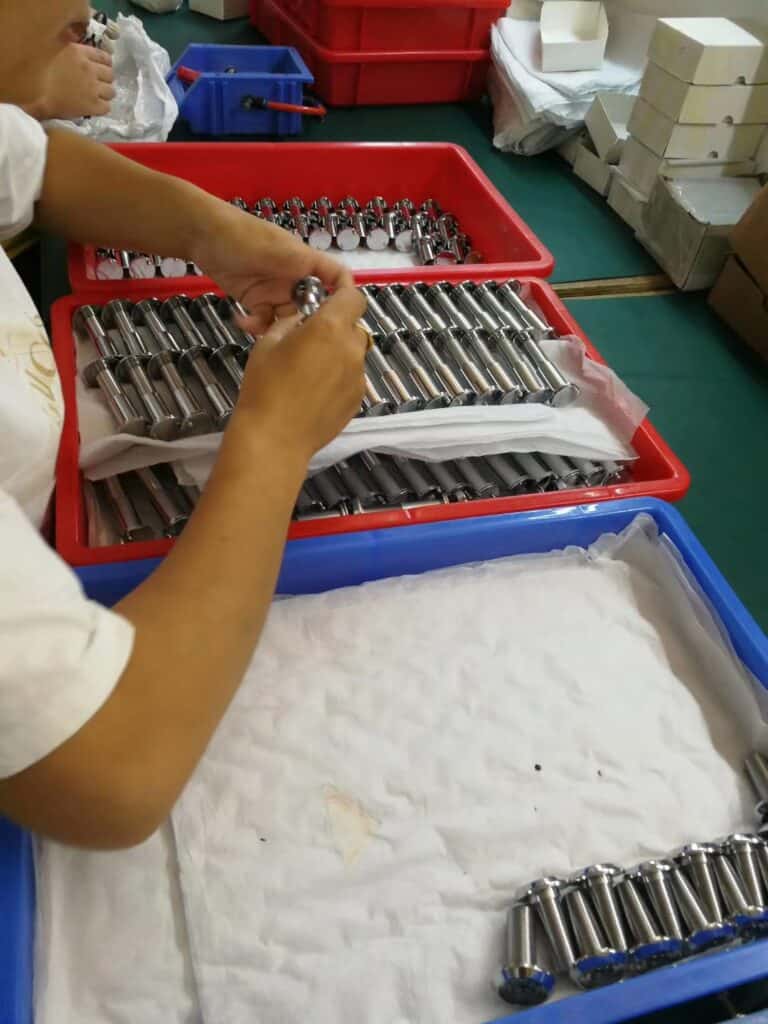
For example, I have seen a lot of factories, in the work instructions take a lot of descriptive language, such as “the surface is smooth” “will be blue cable folded to bend”.
So my question is: How smooth is smooth? How many degrees is a bend?
In the production world, everything can and must be presented in data. If not, in addition to not being able to ensure the quality and stability of production, it will also bring the problem of the lack of testing standards.
3. Finished product inspection standards
In many factories, QC (Quality Control) is often an ornament.
For example, a factory director himself confessed that in the past, their QC and production often quarrel, QC said “the quality of this batch of products is not good” production but said “the equipment situation is like this, you can you on”.
In the end, the problem can only be pushed to the business, and even to the customer, so that the customer is forced to accept the defective products.
But this is not the most damaging, the most damaging is the factory QC corpse, and even production collusion.
Quality control/quality inspection personnel should have been in the production of the opposite side.
So from the perspective of procurement and supply chain managers, our third key concern when looking at the factory, naturally, is whether the other party has clear finished product inspection standards, and whether the implementation of the finished product inspection process and records are in place.
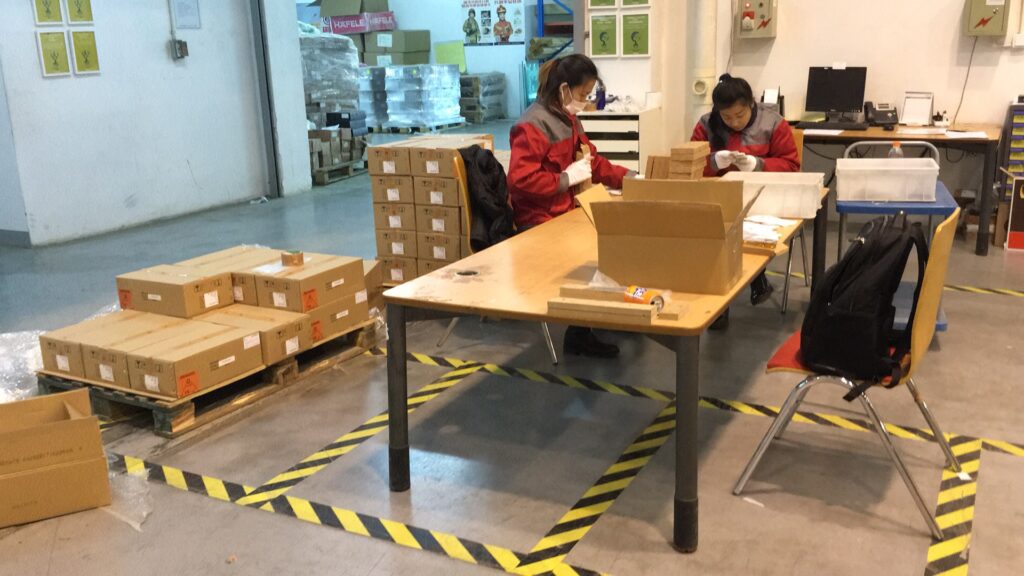
What is a clear finished product inspection standards? Share another real case.
We should have seen the yellow sticky notes, how do you judge the quality of a sticky note is good or bad? Tear it off and paste it onto an item to see if it is good or not and if it sticks steadily.
But from the factory’s point of view, can you use this method of product quality inspection? Definitely not.
As I said before, “everything can and must be presented in data”.
Comprehensive above, around the incoming material inspection specifications, production process control and finished product inspection standards, we can naturally be targeted when looking at the factory, rather than being reduced to a horse and buggy.
Sourcing agency and supply chain management
Regardless of the procurement agency or supply chain management services, there is a common feature: selling is not a product, but a service.
What is the biggest problem of service?
- Invisible and untouchable. Unlike physical products, we are at least able to take photos and videos for customers to see. Or send a sample to the customer, so that he can feel it.
- Non-standard. Just as Tony teacher haircut charges 69, but Jacky director to charge 99, what is the difference between them? It is difficult to say a reason.
This problem, once also troubled us for a long time, until later I found the following entry points.
If I do not have a way to quantify the results, then quantify the process.
If I do not have a way to show the product, then show the case.
If I do not have a way to reflect the service, then reflect the evaluation.
We SDH hardware as a professional architectural hardware manufacturer and supplier, we have produced door hardware for many big brands for more than 10 years, including mortise door lock, euro brass lock cylinder, stainless steel lever handle, butt hinge, and concealed hinge. Due to our experience with many international hardware brands, our service, product quality, and architectural hardware knowledge will not let you upset.
Please contact us for any door hardware inquiries:
Email: info@sdhhardware.com
Mobile/Whatsapp: +86 13693395023