When checking the hardware quality, we usually take the mechanical function and surface as the most important top 2 factors, we can check the mechanical function according to the EN standard or UL standard, but when referring to the surface, it’s hard to define the standard. So let’s talk about how to make the perfect surface for #doorconcealedhinge
Choose a good die-casting material: A good zinc alloy material contains 96% zinc, 3.9% aluminum, 0.6% magnesium and 0.5% impurities. Generally, the material used in Wenzhou factory does not contain magnesium. The remaining gum mouth and miscellaneous packages after die-casting cannot be returned to the furnace. The remaining die-casting material after taking down the workpiece must add other elements and then return to the furnace.
Ensure good die-casting quality: When determining the quality of die-casting parts, we must look at the die-casting blank parts, polishing can cover up the die-casting flowers, so that the naked eye can not see, but can not solve the problem of die-casting flowers. Inspection just die-casting good workpiece, white, uniform filiform pattern, indicating good die-casting quality, the workpiece surface is cloudy, there are stars, the die-casting quality is not good.
Plating and organic layer protection is also important, such as keeping the plating tank and solution clean, spraying workshop clean, etc. Not the longer plating time is better, the longer time also increases the chance of pitting, all good polished parts can shorten the plating time, as long as the salt spray requirements can be met.
The protection work in the logistics process is also important, the surface hardness of most products can only reach 2H, bad transit tools will cause the surface of the product to appear bumping injury.
Common problems in the surface inspection of electroplated parts
Pockmark: Most of the pockmarks are caused by the powder layer in the spraying workshop. It may also be caused by unclean pretreatment or unclean solution of basic plating. Plating link usually does not appear pitting, because the plating time is short, for example, plating imitation gold only takes 25-30 seconds, the impurities in the solution can not be firmly adsorbed on the surface of the substrate, the plated parts have been out of the tank.
Air bubbles: generally caused by poor die-casting. If there are sand holes or gaps on the die casting, bubbles will be formed when the product is sealed and dried with lacquer. The bubbles can be reduced by lowering the baking temperature of the lacquer layer, but this method is not reliable. Lowering the baking temperature will also reduce the solidity of the lacquer layer adhesion, and the product will be susceptible to dampness that will cause the lacquer layer to fall off. Therefore, the most fundamental solution is to ensure the quality of die casting. And the oven temperature should be kept at 180℃ when the lacquer layer is baked, and the workpiece temperature should be kept at 155-165℃.
Watermark: It is caused by unclean deionized water used in plating link. The deionized water used for plating should ensure that the electrical conductivity does not exceed 5μS/CM3, and the resistivity should also be maintained at no more than 50μS/CM3 during production. deionized water exceeding 5μS/CM3 can be used for pre-treatment.
Discoloration: Seal the paint in time after plating to avoid oxidation of the plating layer as much as possible. When changing hangers before painting, you need to pay attention to use gloves.
The reason why Guangzhou plating quality is better than Wenzhou
Guangzhou electroplating process is better, many of them are brought by Hong Kong people, and the used potion is good and the thickness of plating is guaranteed
Most of the factory’s spraying workshop is dust-free, and the products have less pockmarks.
The polishing quality in Guangdong is good, which can shorten the plating time. The longer the plating time is, the greater the possibility of pitting.
Why is it hard to plating for aluminum alloy?
Aluminum alloy is difficult to die-cast and cannot provide high quality die-casting, so it is difficult to plating. Due to the high melting point of aluminum alloy, generally only cold chamber die casting machine can be used for die casting, so the temperature of raw material cannot be guaranteed during the feeding process, and the more the temperature drops, the more difficult it is to make good die castings.
About plating thickness
At present, the highest standard of plating is the Japanese plating requirement. The total thickness of general plating is 20μm (not containing the thickness of machine layer). The thickness of copper plating (alkaline copper + coke copper + acid copper) is 12μm (plating time 1000 seconds), and the thickness of nickel plating is 8μm (plating time 600 seconds). Chrome plating deposition speed is slower, generally 2 minutes can reach 0.1-0.12μm, usually the thickness of the chromium layer is greater than 0.1μm, the best can reach 0.2-0.3μm. other plating layer are very thin.
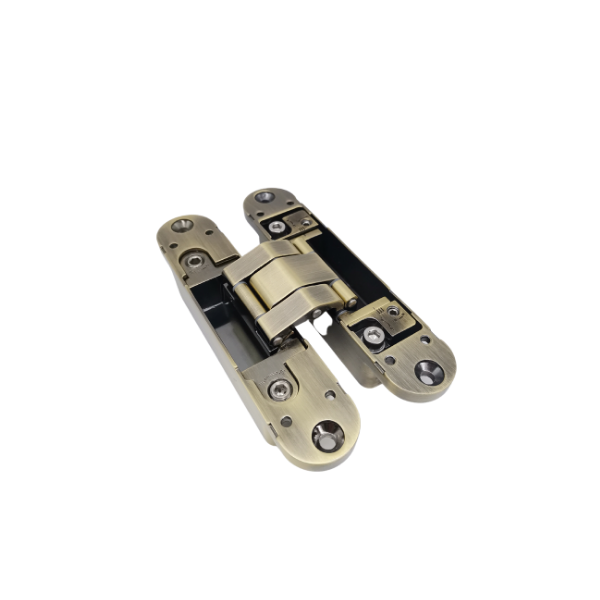
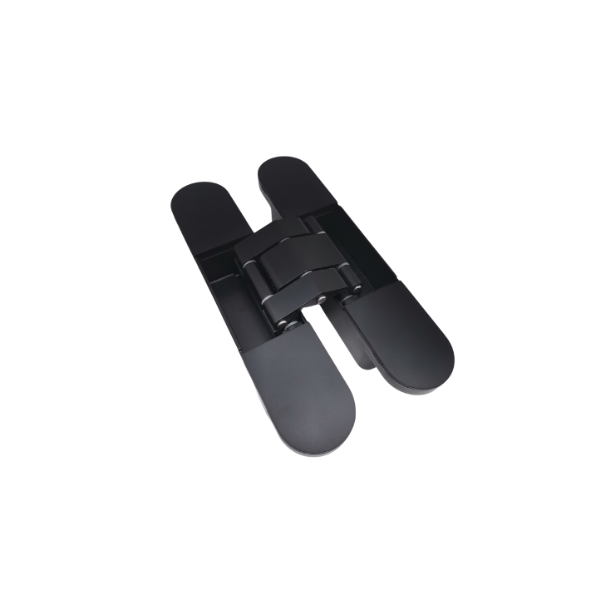
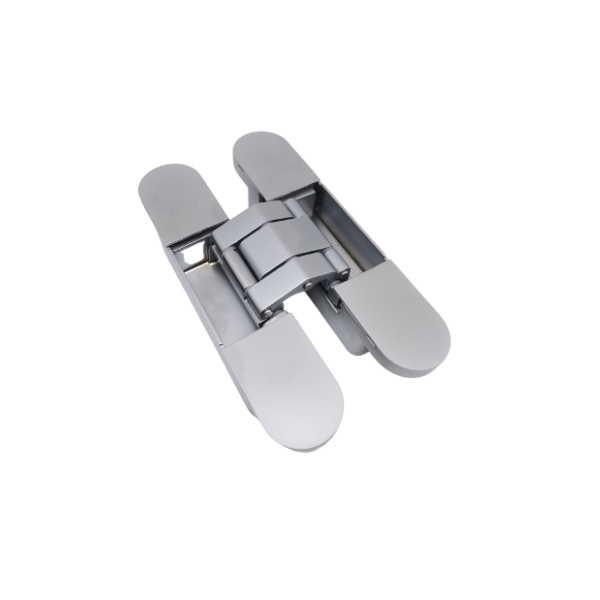
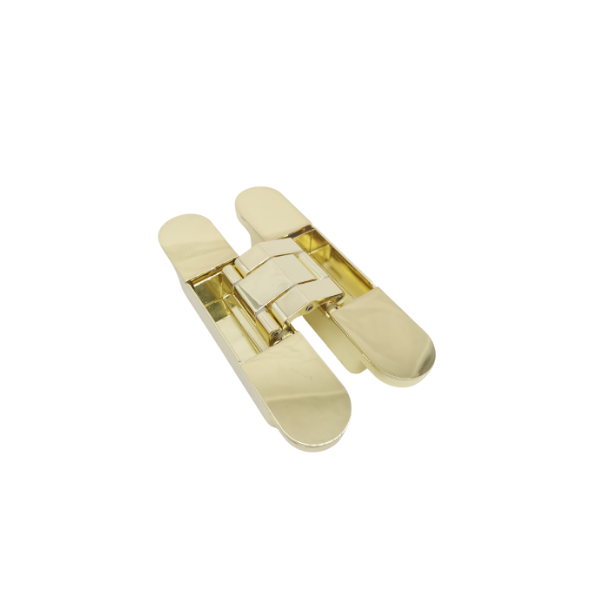
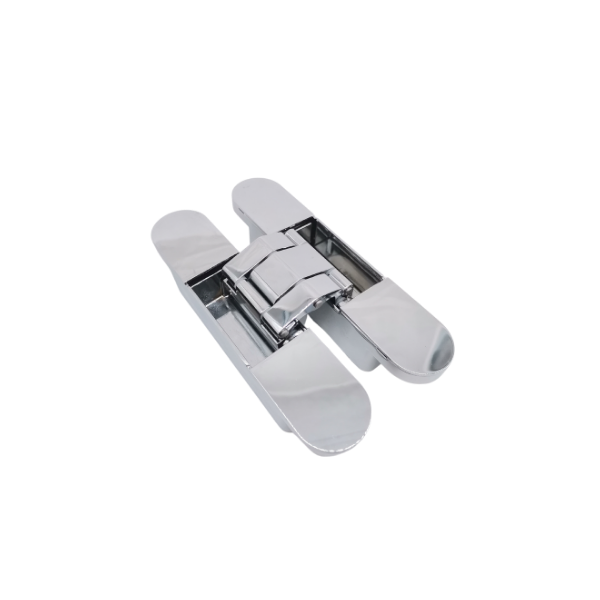
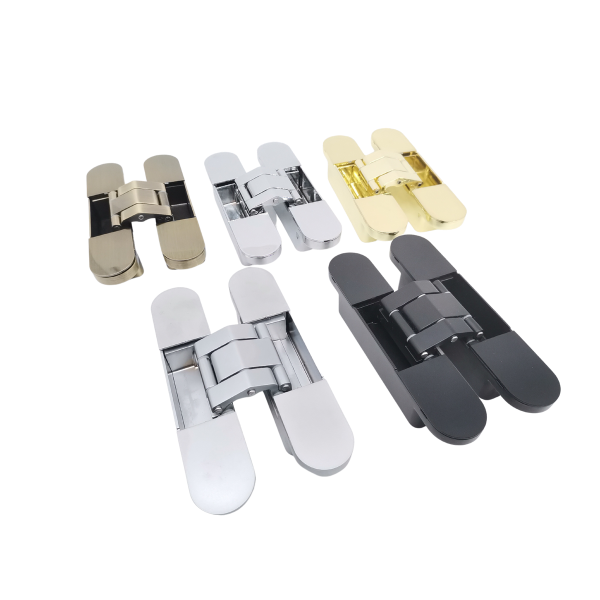