The production of 3D adjustable concealed hinges is a complex process involving multiple manufacturing stages. These hinges are designed to offer flexibility and precise door adjustments, ensuring smooth and reliable operation. This article outlines the key steps involved in the production process of 3D adjustable concealed hinges.
There are many materials for making hinges,such as stainless steel, zinc alloy and aluminium. This article mainly introduces the production process of zinc alloy 3D adjustable concealed hinges. Zinc alloys are used for the production of these hinges due to their excellent mechanical properties and corrosion resistance. Zinc alloys, on the other hand, are commonly used for the die-casting process, as they can be molded into complex shapes with high precision.
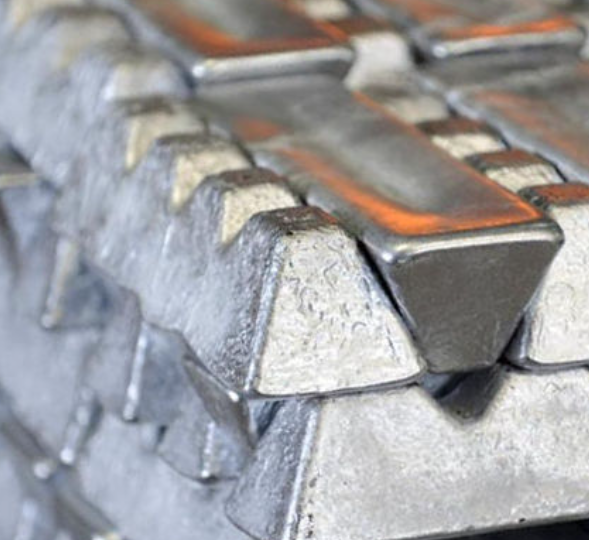
Die-Casting
Die casting is a manufacturing process where molten metal is injected into a mold under high pressure to form a specific shape. For the 3D Adjustable Hidden Hinge, die casting is used to produce the complex, fine parts of the hinge, such as the hinge body and movable components.
The die casting process begins by melting the selected metal alloy in a furnace. The molten metal is then poured into a pre-made mold, which determines the shape of the hinge component. High pressure is applied to ensure that the molten metal fills all cavities of the mold and solidifies into the desired shape. This method allows for the precise and consistent production of parts with tight tolerances, which is critical to the proper functioning of the hinge.
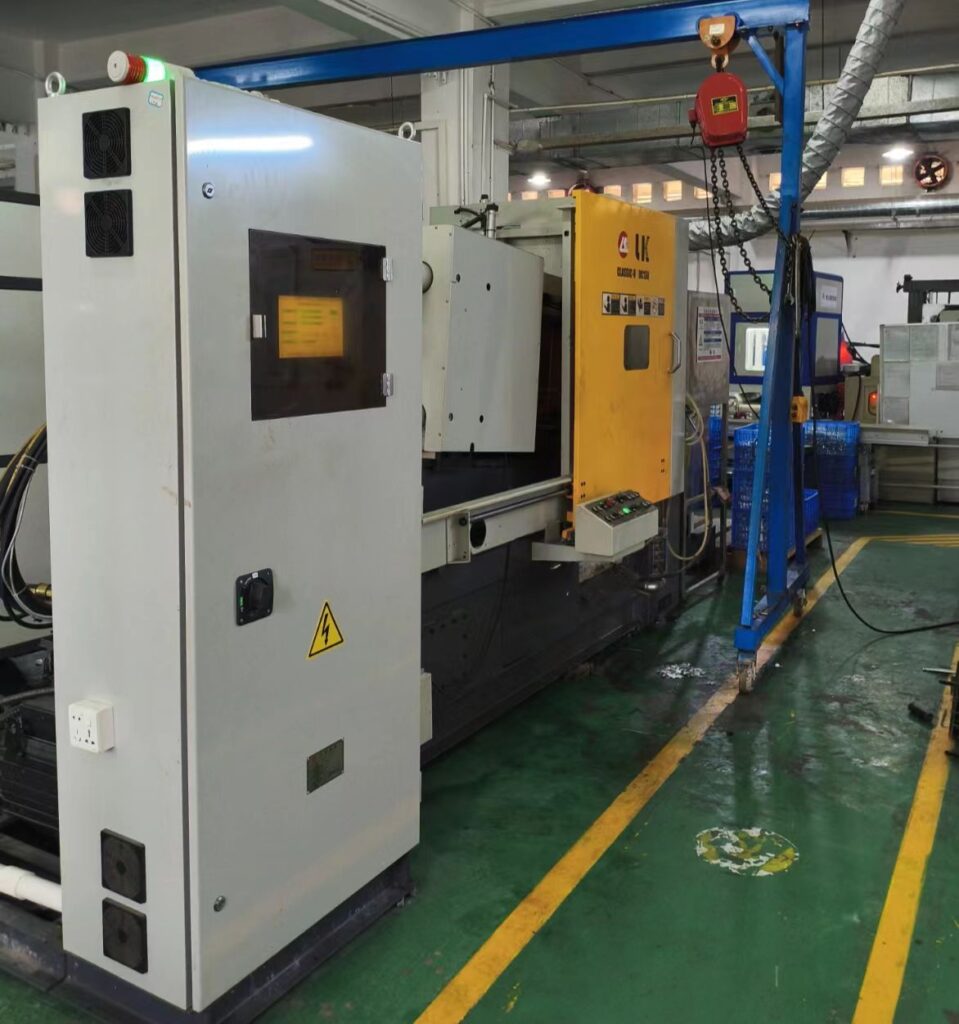
Machining
After the die-casting process is completed, the next step is machining. For example, deburring, tapping, punching, etc. Use machines to tap the die-cast parts that need threads to facilitate the fixing of screws. Burrs on the product are removed manually by grinding with tools such as burr cutters. Punching is done by machine for products where the opening position does not open properly after die casting. Mechanical presses apply force to the punch and die to remove excess material from the part, ensuring that the holes on the product are properly opened and used to accommodate screws, pins and other fasteners.
Polishing
Polishing is a finishing process that smooths the surface of a metal component to improve its appearance and remove any rough edges or burrs from die casting.
Polishing is usually performed using a specialized polishing machine equipped with a grinding wheel or belt. The component is placed in the machine and a polishing tool is used to grind away any imperfections on the surface. The result is a smooth, shiny surface that enhances the beauty of the hinge and prepares it for electroplating. Polishing can also help improve the overall quality of the hinge by removing any surface defects that may affect its function or durability.
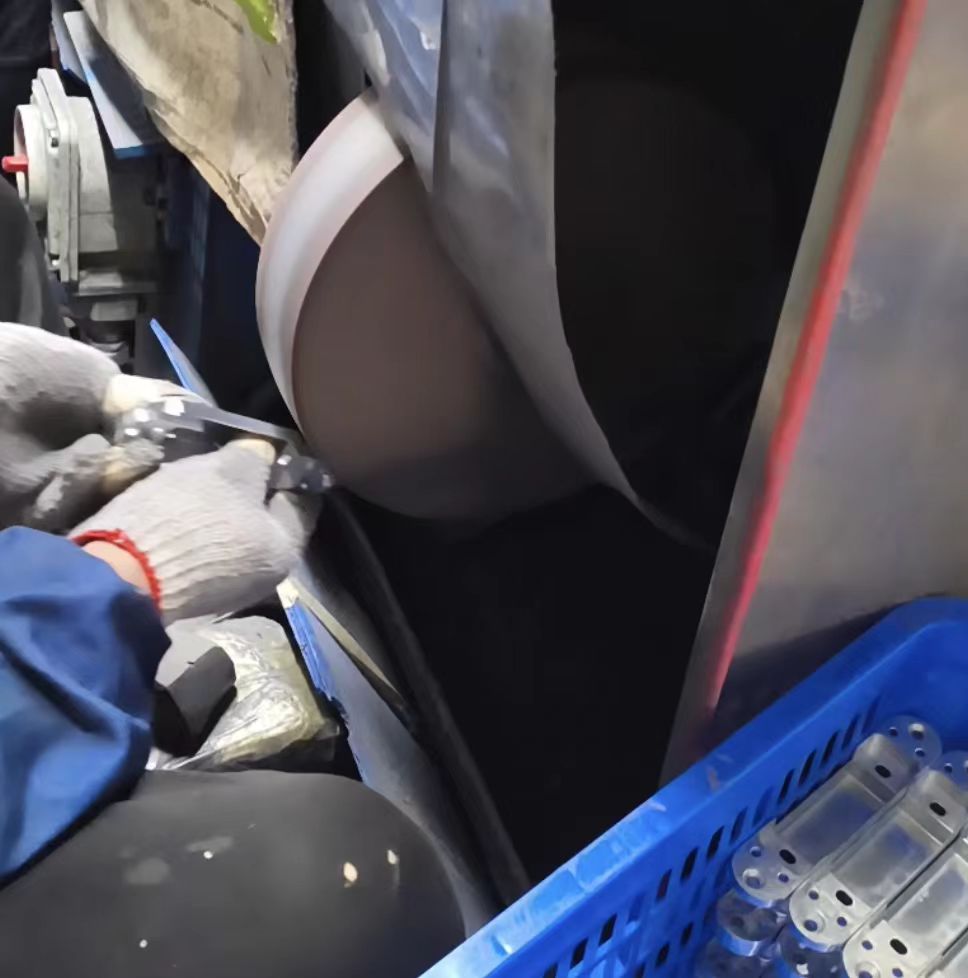
Electroplating
Surface treatment
After polishing, the hinge components are subjected to surface covering, such as electroplating and PVD treatment. Electroplating is the process of depositing a thin layer of metal on the surface of the hinge component through an electrochemical reaction. This is usually done to improve the appearance of the part, provide a protective coating and enhance its corrosion resistance.
For 3D adjustable hidden hinges, common electroplating surfaces include chrome plating, nickel plating and zinc plating.
After the last step of “nickel plating” in basic electroplating (copper plating & nickel plating), other plating colors can be selected, such as the AB, AC, satin chrome, gold, etc. The final painting process completes the electroplating.
The electroplating process involves immersing the hinge component in a plating solution containing the metal to be deposited. An electric current passes through the solution, causing the metal to adhere to the surface of the component. After surface treatment, it enters the next stage of production.
Quality Inspection
After the plating process is complete, the next step is quality inspection. Quality control is critical to the production of 3D adjustable hidden hinges to ensure that each component meets the required specifications and standards. Inspection includes checking the physical dimensions of the parts, verifying the quality of the plating, etc.
Various testing methods can be used, including visual inspection, dimensional measurement. Carefully inspect the hinge parts for any defects such as cracks, scratches, or uneven plating. Check the dimensions against the design specifications to ensure that they meet the required tolerances.
Assembly
The final step in the production process is assembly. During the assembly phase, the individual components of the 3D adjustable concealed hinge are brought together to form a complete product. This typically involves installing pins, screws, and adjustment mechanisms.
The hinge components are carefully aligned and secured using screws or pins. The adjustment mechanism is tested to ensure that it allows smooth and precise movement, allowing the door to be adjusted in three dimensions – vertically, horizontally, and in depth. Once the hinge is fully assembled, a final quality check is performed to ensure that all components are functioning properly.
After assembly, the 3D adjustable concealed hinge and accessories (screws, Allen keys, and covers) are packaged and prepared for shipment. They are typically packed in cartons, which can be customized to the customer’s requirements.
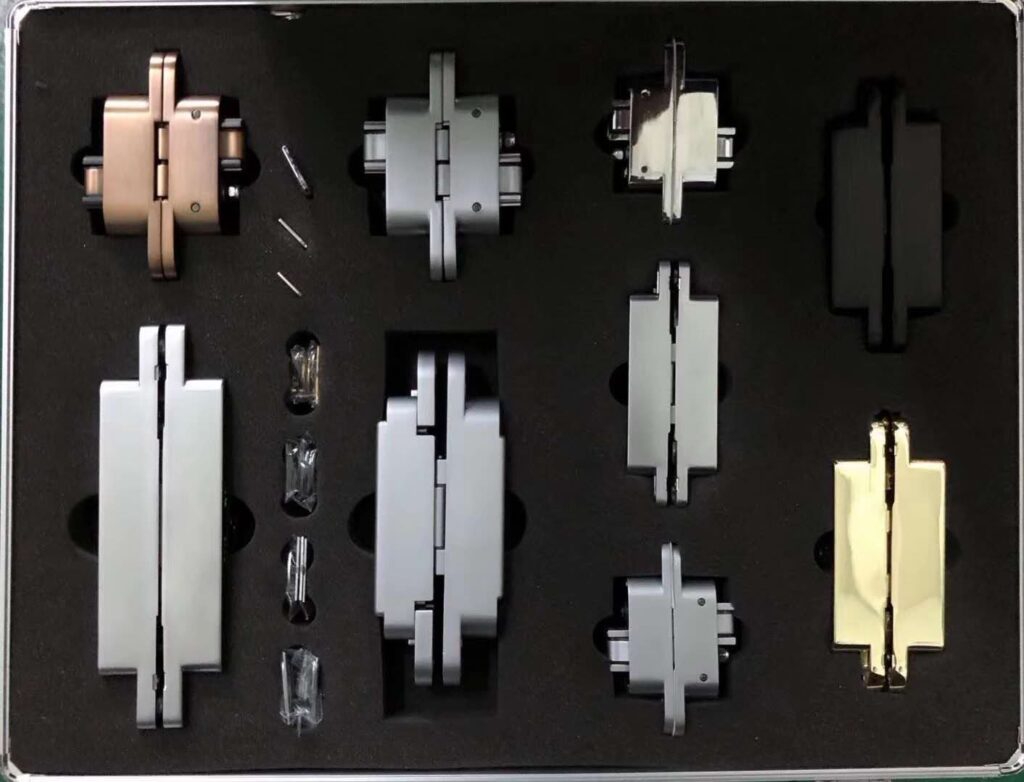
Conclusion
The production of 3D adjustable concealed hinges involves a series of well-coordinated steps, from material selection to final assembly. Each stage plays a vital role in ensuring the quality and performance of the finished product. By following a strict production process, manufacturers can produce high-quality 3D adjustable concealed hinges that provide precision, durability and reliability for a variety of applications.
If you have any questions, please contact us.