Metal surface treatment plays a crucial role in enhancing the performance and longevity of various door hardware products. By applying different techniques, manufacturers can improve resistance to corrosion, wear, and other environmental factors. This article provides an overview of the main metal surface treatment processes of door hardware.
Electroplating: Enhancing Surface Durability
Electroplating is a process that uses electrolysis to deposit a thin layer of metal onto the surface of a base material. The process involves immersing the workpiece (cathode) in an electrolyte solution with metal ions, while the coating metal serves as the anode. A direct current is passed through the solution, and metal ions are reduced onto the surface of the workpiece, forming a protective coating.
Common metals used for electroplating include zinc, nickel, copper, and chromium. Electroplating provides several benefits: it enhances corrosion resistance, improves hardness, and adds aesthetic value to the surface. For example, zinc plating is often used to prevent rusting of steel, while nickel plating offers wear resistance and a bright, polished finish. Chromium plating, known for its hardness and corrosion resistance, is used for both decorative and functional purposes.
After the last step of “nickel plating” in basic electroplating (copper plating & nickel plating), other plating colors can be selected, such as the AB, AC, satin chrome, gold, satin brass, etc. The final painting process completes the electroplating.
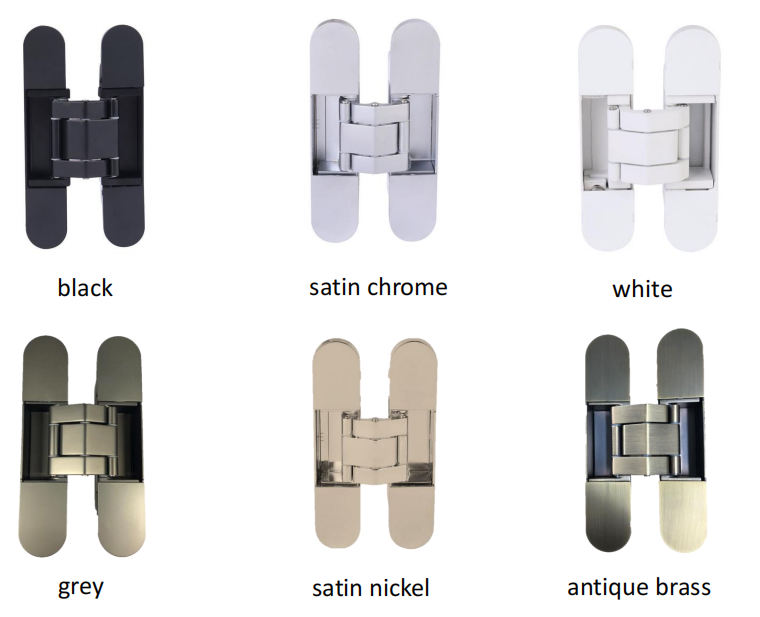
Oxidation: Protecting Metal Surfaces
Oxidation treatment, commonly known as “bluing” in steel parts, involves exposing metal to an oxidizing solution that forms a thin, dense oxide layer on the surface. This protective layer improves the metal’s resistance to corrosion and wear. Steel oxidation is typically done through alkaline or acid solutions, with sodium hydroxide and nitrite salts being common agents in the process. The resulting oxide film not only enhances corrosion resistance but also reduces internal stresses, providing greater stability to the material.
While oxidation can be applied to steel, aluminum and aluminum alloys can also undergo oxidation, though the processes vary. Aluminum oxidation creates a hard, durable layer that is resistant to wear and can also be dyed for aesthetic purposes. Aluminum can undergo anodizing, a type of electrolytic oxidation, which results in a thicker oxide layer that increases corrosion and abrasion resistance.
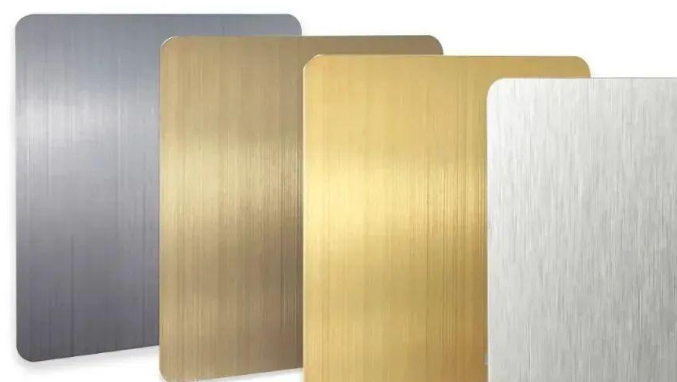
Phosphating: Preparing for Further Coatings
Phosphating is another chemical treatment used to improve the corrosion resistance of metals, particularly steel. In this process, the metal is immersed in a phosphoric acid solution, forming a thin, crystalline phosphate coating on the surface. Phosphating is commonly used as a pre-treatment for painting as it provides better adhesion and improves the durability of the applied coatings.
There are several types of phosphating, including zinc, manganese, and iron phosphating. Zinc phosphating is widely used in automotive applications to prepare steel parts for painting. The phosphated surface also enhances lubrication in applications involving moving parts, such as gears and bearings. Phosphated parts are often used for rust-proofing, particularly in the automotive and construction industries.
Passivation: Enhancing Corrosion Resistance
Passivation refers to the process of treating a metal surface, typically stainless steel, with an acid solution to enhance its natural corrosion resistance. The treatment involves immersing the metal in a solution of nitric acid, which removes free iron and promotes the formation of a protective oxide layer. This oxide layer makes the surface more resistant to rust and other forms of corrosion.
The passivation process is particularly important in industries where metal components are exposed to harsh chemicals or extreme environmental conditions. Stainless steel parts that undergo passivation maintain their aesthetic appearance and perform better over time.
Spray Coating: Protective and Decorative Finishes
Spray coating is a technique that involves applying a layer of paint or other protective coating to the surface of metal parts using a spray gun. The spraying process is either done manually or through automated systems, depending on the scale and complexity of the parts. The coating material can range from traditional paints to more advanced protective coatings like epoxy, polyurethane, or powder coatings.
One of the key benefits of spray coating is its ability to provide a uniform and smooth finish, which enhances both the aesthetic and functional properties of the metal. For example, powder coating, a popular type of spray coating, is used to create a durable, scratch-resistant finish on items like automotive parts and furniture. Spray coatings also provide resistance to weathering, corrosion, and wear, making them suitable for outdoor applications.
PVD Treatment
PVD-Physical Vapor Deposition is a technology that uses the reaction between gases to deposit single or multi-layer films on the surface of various materials or products. It can spray particles with special properties (high strength, wear resistance, heat dissipation, corrosion resistance, etc.) on the parent workpiece with lower performance, making the workpiece perform better.
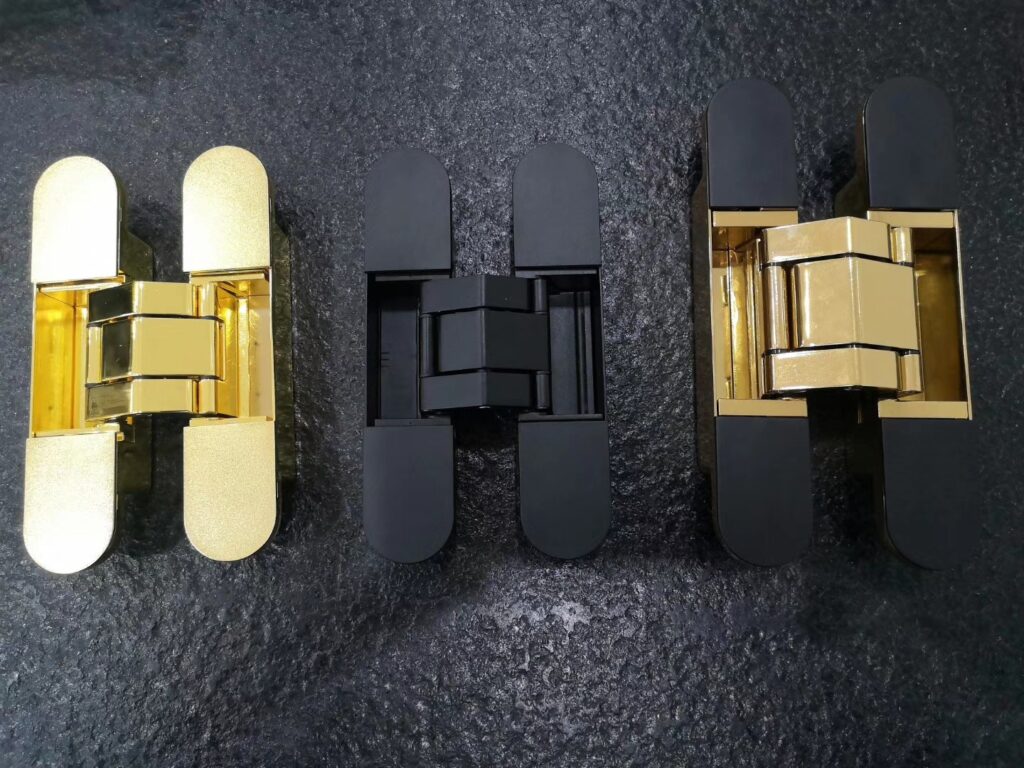
Conclusion
Metal surface treatments significantly improve the performance, longevity, and appearance of door hardware. The most commonly used surface treatment in the door hardware industry is electroplating, which can give the product a variety of finishes. If you have other questions, please contact us.